Вопреки стереотипу о грязном производстве российские металлургические компании уже несколько десятилетий разрабатывают новые технологии и решения, обмениваются опытом и внедряют лучшие мировые экологические практики. В индустрии активно идут обсуждения, что переход к нулевой эмиссии и замкнутому циклу производства может стать реальностью в ближайшие десятилетия. Но так ли это? Насколько мы близки? О том, каким должен быть общий подход и что для этого делают компании уже сегодня — поговорим в материале.
Cодержание статьи
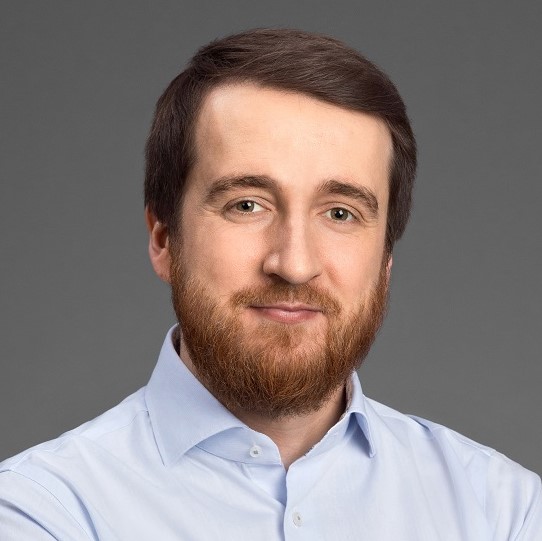
Обзоры, интервью, свежие новости и изменения в законодательстве — оперативно в нашем Telegram-канале. О самых важных событиях — в нашей группе ВКонтакте.
Тенденции экологизации производства
Первыми в мире внедрять природоохранные технологии начали предприятия Европы и Северной Америки в конце 1960-х годов, когда отрасль только начала задумываться о сохранении природы, в мире начали появляться первые очистные сооружения на металлургических предприятиях.
Россия включилась в этот процесс позже, но сейчас отечественные предприятия с точки зрения экологичности находятся на среднемировом уровне, а в чем-то даже превосходят западных конкурентов: в частности, системы рециклинга и очистка бытовых вод от деятельности завода сегодня вызывают повышенный интерес у мировых металлургических компаний.
На протяжении последних десятилетий наблюдаются следующие ключевые направления в экологизации производства:
- Во-первых, внедрение новых технологий по очистке и снижению воздействия на окружающую среду. Хороший пример и одновременно главный тренд сегодня — использование рукавных фильтров, которые позволяют снизить уровень эмиссии в несколько десятков раз по сравнению с технологиями предыдущего поколения.
- Второе глобальное направление — стремление к экономике замкнутого цикла, при которой предприятие повторно использует в производстве разные материалы или продает их на переработку.
Снижение эмиссии
20 лет назад удельная эмиссия вредных веществ в атмосферу от металлургического производства могла превышать показатель в 40 кг на тонну. Сегодня лучшие технологические решения позволяют довести эту цифру до 18 кг на тонну, то есть обеспечить снижение больше, чем в два раза. Ряд российских металлургических предприятий (например, НЛМК) публично озвучили планы по достижению такого уровня удельной эмиссии. Согласно данным компании, по итогам 2021 года эта цифра составила 18,1 кг на тонну, то есть уже практически достигли цели.
Снижение эмиссии достигается прежде всего реконструкцией и строительством новых систем газоочистки. Система работает по принципу пылесоса: вытягивает пыль и газы из технологических процессов, пропускает через рукавный фильтр и выпускает в атмосферу чистый воздух.
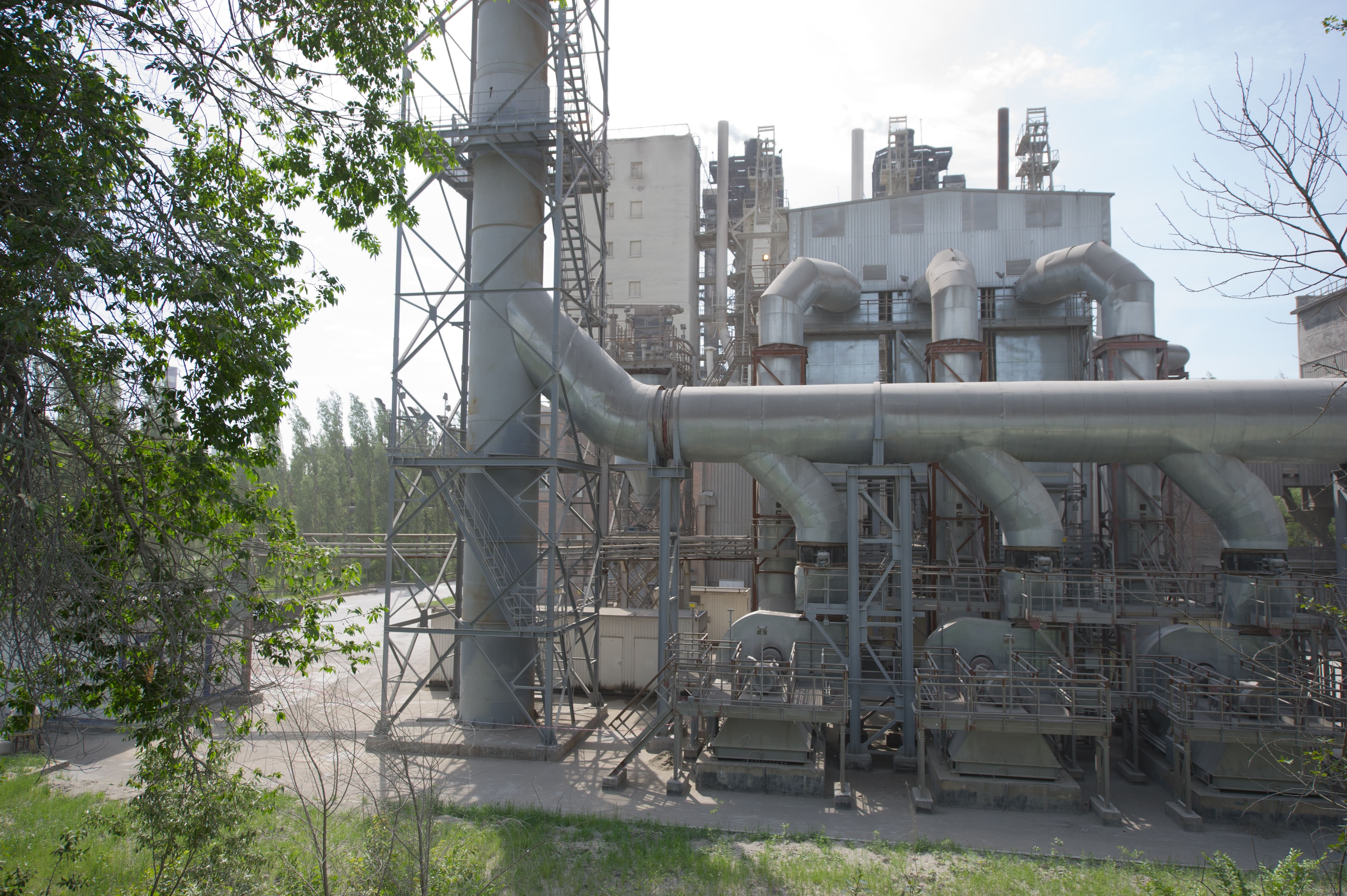
Прогнозируя планы по снижению эмиссии, важно учитывать время на саму реконструкцию систем. На крупных предприятиях их число может достигать нескольких сотен — таким образом, повышая эффективность очистки в 20 или 30 раз на одном объекте, общая эффективность очистки растет не такими впечатляющими темпами. Второй важный момент — современные системы газоочистки не только обеспечивают более эффективное улавливание пыли и газов, но и имеют намного более высокую производительность, способны пропускать через себя больший поток за единицу времени. То есть, показатель удельной эмиссии уменьшается, но абсолютный объем проходящих газов может даже увеличиться.
Полезное использование газов
Повторное использование отходящих газов — важная часть пути к экономике замкнутого цикла, они тоже влияют на значение удельной эмиссии.
Один из передовых типов проектов в этом направлении — станции, работающие на отходящих газах. Если раньше газы, отходящие от конвертеров (так называются агрегаты, производящие сталь), сжигались — это тоже способ очистки, — то теперь эти газы используются для выработки электроэнергии на нужды предприятия. Это дает двойной эффект:
- локально — снижение эмиссии в атмосферу;
- глобально — снижение потребления электроэнергии и, как следствие, экономия энергоносителей (уголь, газ).
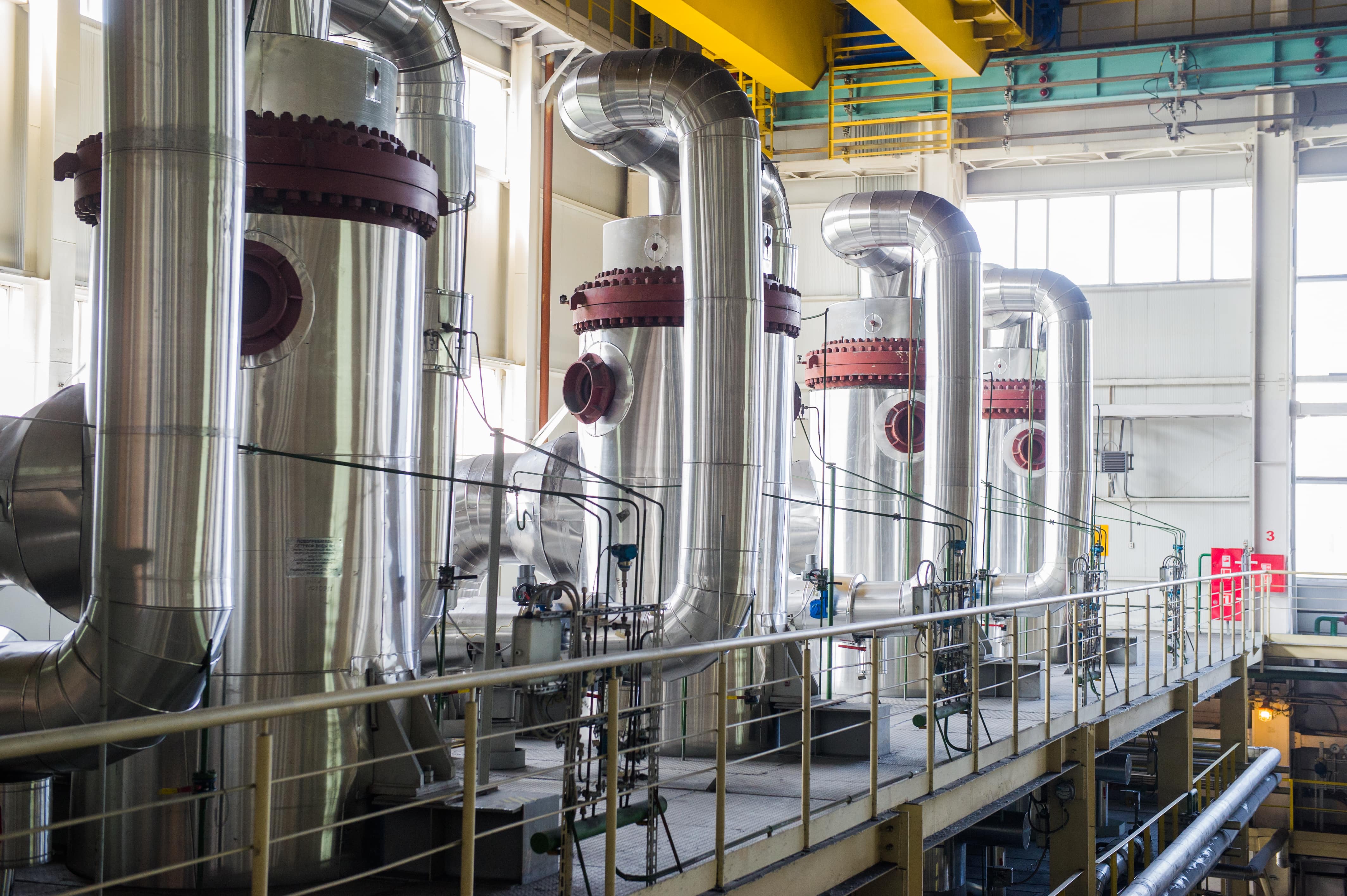
Использование всех возможностей
Чтобы достичь результата, важно искать точки приложения усилий по всей цепочке, в том числе и до непосредственно производства стали. Одна из ключевых инициатив здесь — проекты по повышению содержания железа в руде. Чем оно выше, тем ниже потребление кокса в доменной печи, что, в свою очередь, существенно снижает эмиссию СО2 в атмосферу. Более локальный эффект — от снижения расхода кокса образуется и меньше коксовой пыли.
Повышение содержания железа в руде — фактически более эффективный способ обогащения руды. Здесь существуют разные технологии:
- Во-первых, более эффективные мельницы, отсекающие пустую породу (кремний, песок). Это положительно сказывается на экологичности в том числе с точки зрения логистики: предприятия не тратят ресурсы на перевозку пустой породы и энергию на то, чтобы ее расплавить, и так далее.
- Вторая технология — использование современных способов сепарации полезного железа от пустой породы. Это призвано достичь аналогичной цели — отсечь пустое, увеличить содержание полезного. Сейчас некоторые металлургические компании приближаются к показателю 69% железа в руде — предыдущие технологии позволяли поддерживать эту цифру на уровне 67%, что не кажется большим достижением. На деле это не так: отслеживая динамику, технологи смотрят на десятые, а иногда сотые доли процента. И 2% в этом масштабе — серьезный рывок вперед.
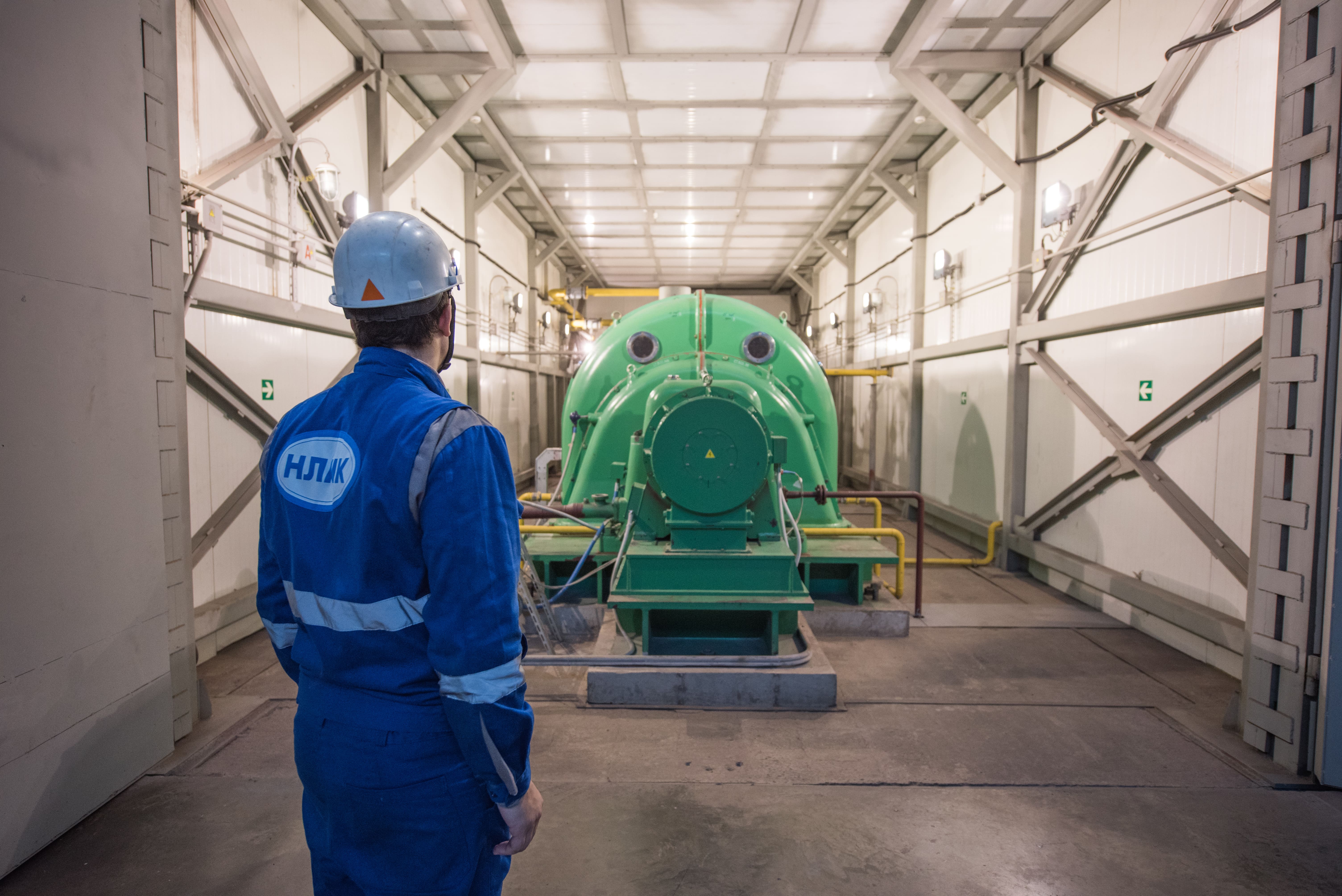
Готовность к переменам
Не всегда нужны революционные технологии — часто для результата достаточно модернизации существующих. Например, те же газоочистные установки за пару десятков лет прошли путь степени остаточной запыленности от 100 мг и более до 5 мг на кубометр, в отдельных случаях сегодня это значение может составлять 1-2 мг на кубометр.
Развиваются и технологии рециклинга. Здесь российские металлургические предприятия не ограничиваются использованием рециркуляции газов на агломерационных фабриках (часть завода, где производится рудный концентрат). Да, задействуя газы повторно, компании достигают серьезного эффекта с точки зрения снижения абсолютного воздействия на окружающую среду, но здесь металлургия уже близка к достижению наилучших возможных показателей. Поэтому что делать дальше? В поисках ответа на этот вопрос многие компании смотрят за пределы производства, на уровень всего города. Иными словами, если раньше металлургические предприятия беспокоила эмиссия «на трубе», то сегодня все больше компаний задумываются о том, что они могут сделать для улучшения качества воздуха за пределами производства: стимулируют использование экологичного транспорта работниками, закупают пылеочистительные машины, которые, работая по принципу пылесоса, убирают пыль с улиц и т. д.
Сотрудничество
Любая стратегия начинается с бенчмаркинга — поиска лучших мировых практик. Это дает свои плоды: так, ряд российских предприятий взяли на вооружение проект австрийской компании — рециркуляцию отходящих газов на агломерационных фабриках.
Еще один пример — использование технологий сероочистки: они будут полезны на аглофабриках, фабриках окомкования и в других цехах. Сейчас некоторые предприятия России оценивают эффективность этих технологий и просчитывают экономический эффект от внедрения на свои площадки.
Более эффективный производственный контроль — еще одна вещь, которой мировые компании вдохновляют российскую металлургию. Например, основной источник негативного воздействия на окружающую среду в производстве кокса — двери коксовой батареи. Проще говоря, с одной стороны сырье загружается, с другой — выталкивается готовый продукт. И давление на эти двери огромно — часто они пропускают газ, поэтому требуется постоянный контроль за состоянием батареи и уровнем эмиссии газа. И если раньше за этим следили сотрудники, то благодаря успешной мировой практике все больше предприятий переходят на видеонаблюдение, часто — с использованием машинного зрения. Алгоритм сам определяет наличие эмиссии и ее степень, при необходимости автоматически уведомляет персонал завода. Все, что остается сделать сотруднику, — уплотнить двери угольной шихтой, чтобы снизить уровень эмиссии.
Часто металлургические компании России сами становятся бенчмарками для конкурентов. Хороший пример — замкнутая система водоснабжения по промышленным стокам, которая используется на предприятии в Липецке. Сам по себе этот проект не новость, но ряд компаний идут дальше и реализуют технологию возврата в производство хозяйственно-бытовых стоков (из душевых, столовых и т. д.). Важно понимать, что металлургические предприятия — это целые города, где работают десятки тысяч человек, поэтому и эффект от очистки бытовых вод достигается существенный. На сегодняшний день это уникальный проект: обывателю может показаться, что вода от металлургического производства грязнее, чем бытовая вода от деятельности человека. На самом деле все ровно наоборот: очистка производственных вод — давно известный и обкатанный процесс, к тому же они меньше влияют на жизнь человека. Бытовые воды — это органика, которую сложнее очистить и обеззаразить. И успешные проекты в этой области, реализованные российскими компаниями, вызывают интерес у коллег по всему миру.
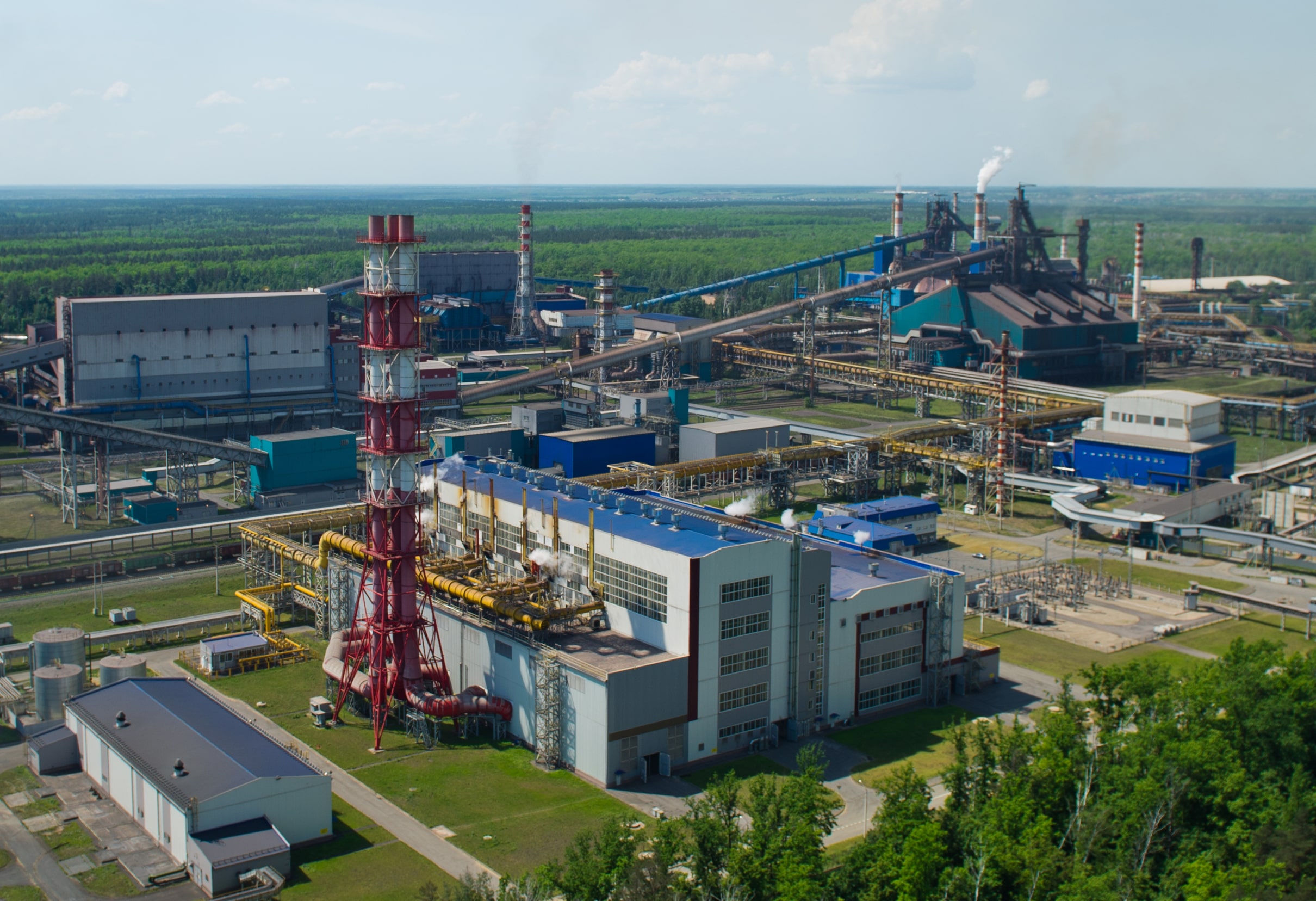
Главные выводы
Цель достичь нулевой эмиссии вполне реальна: большинство технологий для этого уже разработано. Конечно, какие-то решения предстоит создать, но есть еще один не менее важный вопрос — доступность технологий. Быть экологичным все еще дорого: только одна система газоочистки доменной печи может стоить от нескольких десятков миллионов до миллиардов рублей. А на некоторых предприятиях таких установок более пятисот. Но технологии будут разработаны, а деньги получится найти. Куда важнее другое — осознанность и нацеленность предприятий на достижение «нуля». Это комплексный вопрос: нужно не просто снижать эмиссию, но и более эффективно распоряжаться ресурсами и сырьем, потреблять меньше и использовать каждую условную тонну руды на максимум. И когда вся индустрия будет смотреть на это именно так, объединяться для совместной реализации экологических проектов и делиться своим опытом с коллегами, достижение цели «0» станет делом техники.
Напишите, пожалуйста