Разработанная в послевоенные годы японским автогигантом Toyota производственная система (Toyota Production System, TPS) позволила компании занять лидирующие позиции на мировом рынке и была проинтерпретирована и адаптирована американскими менеджерами и названа «бережливым производством» (lean production, lean manufacturing). Простота системы, высокая эффективность и четкие алгоритмы внедрения сделали ее одним из наиболее популярных систем в настоящее время, особенно на высококонкурентных и высокотехнологичных рынках. А одним из самых эффективных инструментов бережливого производства стала система 5S. Подробно об этой системе и том, как ее внедрить, расскажем в данной статье.
Cодержание статьи
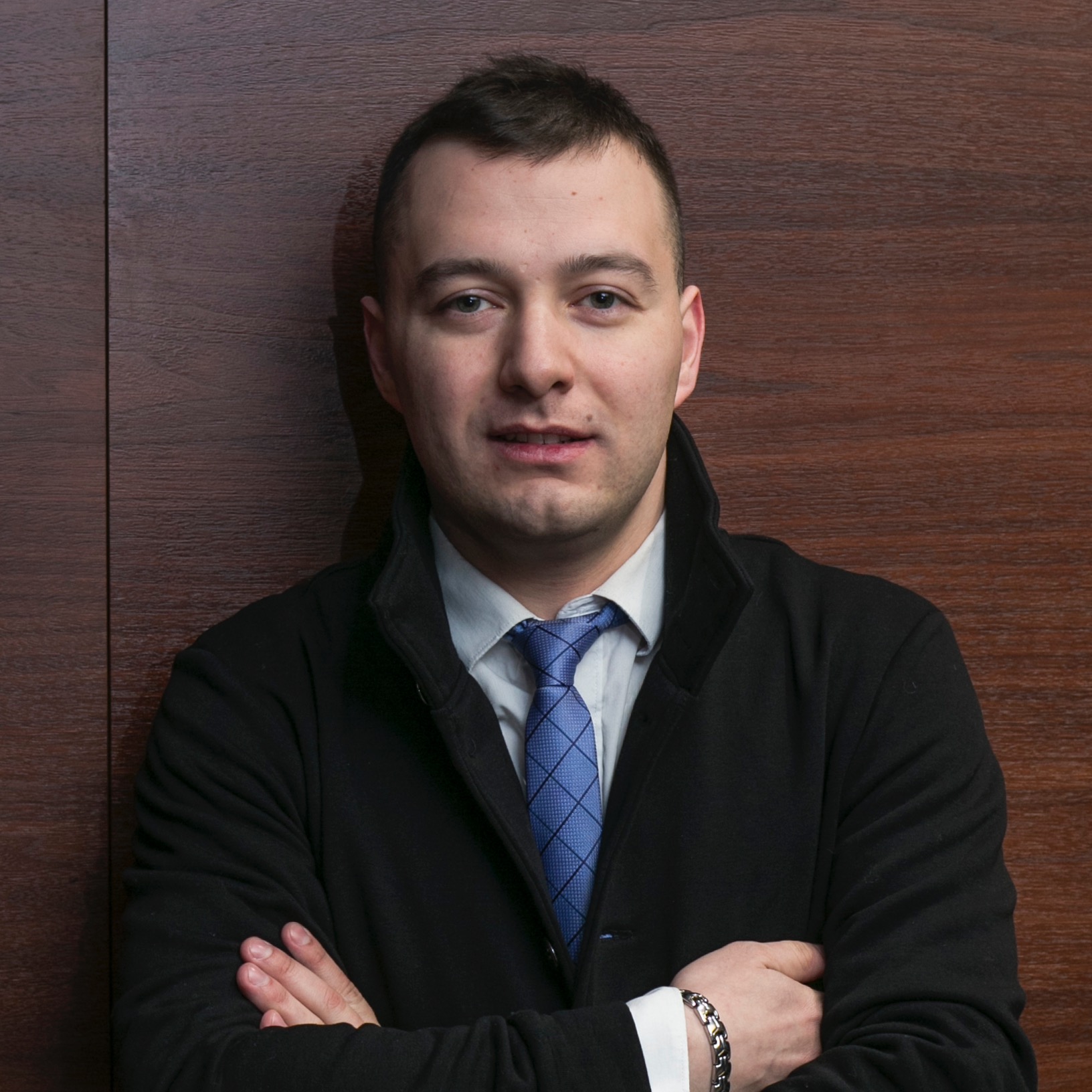
Обзоры, интервью, свежие новости и изменения в законодательстве — оперативно в нашем Telegram-канале. О самых важных событиях — в нашей группе ВКонтакте.
Что такое бережливое производство?
Бережливое производство неразрывно связано с мерами по охране труда и представляет собой «мягкие» способы (напомним, «жесткие» — прописанные в законодательных актах, инструкциях и нормах) обеспечения безопасных условий труда через внедрение идеологии безопасного поведения и оптимальной организации рабочих процессов на производстве или в офисе. Инструменты бережливого производства подразумевают создание и внедрение не только детальных инструкций поведения работников в той или иной рабочей ситуации, но и организацию рабочего места, рабочего пространства, которые позволяют минимизировать риски, связанные с производственными и рабочим процессами, с «человеческим фактором».
В соответствии с концепцией бережливого потребления всю деятельность предприятия можно оценить с точки зрения ценности для потребителя: операции и процессы, ценные для потребителя и операции и процессы, не представляющие никакой ценности для потребителя. Например, для потребителя ценностью является только качество товара или услуги, но косвенные издержки, связанные с браком, арендой складских помещений, оплатой сверхурочных, больничных, другие потери, которые несет предприятие в процессе производства продукта и также включаются в цену, которую платит потребитель, но не представляют для него никакой ценности.
Соответственно, все, что не представляет собой ценности для потребителя — представляет собой ущерб и для потребителя, и для компании, и должно быть устранено из рабочего процесса предприятия. Источники ущерба и потерь предприятия согласно данной концепции можно условно разделить на технологические, организационные и вызванные человеческим фактором.
Основные задачи, которые можно решать с помощью инструментов бережливого производства:
- сокращение затрат (сырьевых, трудовых, производственных);
- сокращение производственных и складских площадей;
- сбалансированное соотношение качества и стоимости продукта;
- минимизация рисков, связанных с человеческим фактором;
- обеспечение оптимальных, максимально безопасных условий труда для всех сотрудников предприятия.
Бережливое производство объединяет ряд инструментов, методов и систем, некоторые из которых уже выделились в самостоятельные концепции управления: кайдзен, канбан, метод «точно-вовремя» (Just-in-Time), poka-yoke («защита от дурака» или принцип нулевой ошибки) и др., однако наиболее популярным и близким к сфере охраны труда инструментом является система организации рабочего пространства 5S.
Система организации рабочего пространства 5S представляет собой пошаговый алгоритм создания наиболее удобного и эффективного с точки зрения выполняемых сотрудником функций, рабочего места, поддержания порядка на рабочем месте и укрепления дисциплины. С точки зрения производства система помогает улучшать качество продукции, снижать количество дефектов. С точки зрения охраны труда система позволяет оптимизировать работу сотрудников, повысить производительность труда, сделать работу сотрудников психологически и физически комфортной и безопасной.
Система 5S является обязательной для выполнения всеми сотрудниками: от уборщицы до генерального директора, и представляет собой последовательное выполнение пяти шагов: сэири, «сортировка» (整理); сэитон, «соблюдение порядка» (整頓); сэисо, "содержание в чистоте"(清掃); сэикэцу, "стандартизация«(清潔); сицукэ, «постоянное совершенствование» (躾).
Шаг 1. «Сортировка»
Этот шаг подразумевает четкое разделение вещей и предметов, находящихся на рабочем месте, на нужные, нужные иногда и ненужные. На рабочем месте должны остаться только тем предметы и документы, которые используются в работе. Если этот принцип применяется для аудита текущего рабочего пространства, то для всех «ненужных» вещей находят применение: продать, передать в другие отделы или другим сотрудникам.
Шаг 2. «Соблюдение порядка»
Здесь важно четко определить места для каждого инструмента, приспособления, предмета или документа на рабочем месте сотрудника. Для определения места используются принципы эргономики, например, справа на столе должны лежать те предметы, которые человек берет правой рукой, в нижних ящиках — те предметы, которые человек использует реже и т.д. Данный принцип призван экономить время, умственные и эмоциональные усилия сотрудника, а также обеспечивать безопасность сотрудника на производстве. Предметы должно быть на видном месте, их должно быть легко взять, легко использовать, легко положить на место.
Шаг 3. «Содержание в чистоте»
Этот шаг предполагает, что на рабочем месте должна поддерживаться постоянная чистота. На производственных участках рабочее пространство делится на зоны, для каждой из которых устанавливается точное время уборки и проверки. Данный принцип должен обеспечить минимизацию ошибок, дефектов на производстве, а также создать приятную для сотрудника рабочую атмосферу.
Шаг 4. «Стандартизация»
Он заключается в создании инструкций, схем, планов, описаний по «сортировке», «порядку» и «чистоте». Данные документы, с одной стороны, помогают каждому сотруднику организовать свое рабочее место, с другой — фиксируют инструменты контроля за соблюдением этих трех принципов, а также фиксируют штрафные и поощрительные санкции.
Шаг 5. «Постоянное совершенствование»
Процесс использования системы 5S зацикливается посредством развития самодисциплины у сотрудников, доведения навыков управления своим рабочим местом до автоматизма и совершенствования системы управления рабочим местом. Реализация данного принципа включает в себя обучение сотрудников (тренинги, игры, использование очков виртуальной реальности для симуляции рабочих процессов), проведение регулярных аудитов рабочего пространства, постоянный поиск возможных оптимизаций. В случае травматизма на производстве, несчастных случаев, ошибок в рабочем процессе пересматривается вся система организации рабочего пространства. В некоторых компаниях принято делать фотографии или видео «до» и «после» усовершенствования рабочего места, даже если это всего лишь изменение порядка, в котором стоят папки с документами или изменение цвета стикеров для записей на рабочем столе.
Как внедрить систему 5S у себя в организации
- Для начала нужно четко определить цель внедрения системы 5S на предприятии (снижение травматизма; уменьшение времени на производство единицы продукта и т.д.).
- Выбрать подход к внедрению системы 5S. «Европейский подход» предполагает, что предприятие приглашает специалиста или консалтинговую группу, которые внедряют, по крайней мере, четыре первых шага системы, а работникам остается только поддерживать систему. Данный подход довольно дорог и, как правило, не дает устойчивых результатов, хоть и позволяет внедрить систему довольно быстро; «восточный подход» предполагает обучение сотрудников, разъяснение сути системы, целей и тех позитивных изменений на предприятии, которые принесет внедрение системы. Далее работникам предоставляется возможность самими организовать рабочие места, а менеджеры предприятия осуществляют текущие консультации работников, контроль и поощрения. Данный метод требует гораздо большего времени для внедрения системы, однако он малозатратен и дает устойчивый результат.
- Создать рабочую группу. Ее возглавляет руководитель предприятия и входят ключевые специалисты из каждого отдела, цеха, участка и т.д. Для начала система может быть внедрена не во всем предприятии, а на «пилотных» участках, но в любом случае, руководители предприятия должны принимать участие в реализации системы. Члены рабочей группы выполняют следующие функции:
- собирают данные о существующих на их участке проблемах (захламленность, потери времени при поиске оборудования, документов, простои, конфликты в коллективе, травматизм и пр.);
- составляют графики развертывания системы 5S на своем участке в соответствии с общим планом предприятия;
- готовят информационные материалы для сотрудников (инфостенды, буклеты, видео, инструкции по поведению в проблемных или небезопасных ситуациях, графики уборки и пр.);
- готовят регулярные отчеты о результатах внедрения системы (фотографии, графики по принципу «до-после», например, вид рабочего места до оптимизации и после).
- Разработка годового плана (дорожной карты) внедрения системы 5S на предприятии. План, как правило, включает в себя обозначение сроков, места и мероприятий по следующим позициям:
- объявление кампании о внедрении системы;
- разработка базовых инструкций для первых этапов;
- назначение и обучение аудиторов, обучение персонала;
- проведение основных этапов внедрения системы;
- проведение аудитов на каждом этапе;
- подведение итогов на каждом этапе;
- составление нового годового плана продвижения системы.
- Объявление всем сотрудникам предприятия о начале кампании по внедрению системы 5S. Это важный шаг, снимающий большую часть психологической нагрузки и сопротивления сотрудников введению новой системы организации труда. Главная цель данного этапа — показать заинтересованность и вовлеченность руководства предприятия, а также дать общую вводную информацию о самой системе и том, как она будет внедряться на предприятии.
- Обучение принципам бережливого производства и системы 5S всех сотрудников предприятия или пилотного участка, вовлеченного в проект. Наиболее бюджетным является «каскадный» метод обучения — сначала обучаются члены рабочей группы и руководители участков, потом они обучают своих подчиненных. Обучение включает в себя подробное объяснение целей внедрения системы, требований к сотрудникам, описание последовательных шагов реализации проекта, информирование о том, кто за что отвечает в рамках данного проекта и с кем можно консультироваться, а также все поощрительные и штрафные методы, которые будут применяться к сотрудникам.
- После прохождения обучения начинается непосредственно процесс внедрения системы по пяти шагам:
- Аудит, анализ достигнутых за год результатов и составление нового плана применение уже внедренной системы 5S. Система 5S предполагает постоянное совершенствование, т.е. улучшение условий труда сотрудников и поиск новых способов снижения потерь для обеспечения максимальной ценности для потребителя, поэтому после внедрения системы 5S на предприятие усилия руководства и рабочей группы должны быть направлены на контроль за ее исполнением, поддержанием мотивации сотрудников в выполнении инструкций и принципов системы, сборе предложений, отзывов, жалоб сотрудников и на их основании разработке новых стандартов и введении их в рабочий процесс.
Шаг 1. Сортировка. Разделите предметы на нужные и ненужные и удалите ненужные. Задачей является научиться определять, видеть и удалять из производственного и управленческого процесса ненужные предметы, делать это постоянно, регулярно, по определенным выработанным правилам. Сортировка направлена на достижение безопасности (устранение атмосферы хаоса, исключения возможности разрушения, порчи, ударов, помех, столкновений, исключения производственного травматизма и др.), качества (исключение вероятности использования бракованных и сломанных материалов, устаревшей информации, документации и т.д.), производительности (повышение эффективности производственной и офисной площади, снижение времени, затрачиваемого на поиск нужных вещей, времени, требуемого на переучет и т.д.), оптимизации складских запасов.
Шаг 2. Соблюдение порядка. Все отобранные предметы разместите в строго определенном и зафиксированном порядке таким образом, чтобы время на их поиск и использование занимало минимум времени и усилий сотрудника. Местоположение предметов фиксируется с помощью разметки, указателей, табличек, карточек, схем и других средств визуализации. Главная задача — обеспечить быстрый, легкий, безопасный доступ к нужным и иногда нужным предметам, а также эстетичность производственной и рабочей среды.
Основные правила размещения предметов: они должны быть на видном месте, их должно быть легко взять, легко использовать, легко вернуть на место.
Шаг 3. Содержание в чистоте. Постоянно поддерживайте рабочие места и предметы в чистоте и постоянной готовности к использованию. Каждый сотрудник должен иметь четкие инструкции по периодичности, методам уборки и методам контроля уборки. Ожидаемые эффекты от проведения мониторинга потенциальных источников загрязнения: сокращение простоев из-за неисправности оборудования и механизмов; улучшение санитарно-гигиенических условий труда; сокращение аварий из-за неисправности оборудования и механизмов; предупреждение аварий, пожаров, несчастных случаев и т.д.
Шаг 4. Стандартизация. Создайте инструкции по сортировке и размещению предметов, уборке рабочего пространства, мерам контроля и поощрения. Инструкции должны быть максимально конкретными, пошаговыми.
Шаг 5. Совершенствование. Каждый из сотрудников несет ответственность за постоянное использование принципов 5S и постоянное улучшение своего рабочего пространства. Предложения по улучшению системы регулярно собираются членами рабочей группы, а сотрудники периодически делают отчеты в формате «до — после» для мониторинга внедрения системы в рабочий процесс.
Трудности при внедрении системы 5S
В то же время, при внедрении системы 5S, российские предприятия сталкиваются с двумя основными проблемами: сопротивление сотрудников нововведениям и недостаточная вовлеченность руководства во внедрение системы на предприятие.
Внедрение любых нововведений в рабочий процесс всегда является стрессом для сотрудников и вызывает осознанное или неосознанное сопротивление, поэтому внедрение системы 5S часто сталкивается с недовольством и страхами сотрудников. Несправедливое распределение нагрузки, переработки, необходимость перестраивать привычное пространство и отказываться от привычных вещей — все эти факторы негативно воспринимаются работниками.
Очевидно также, что российский, японский, американский менталитеты различаются и сотрудники российских предприятий не видят смысла работать на «цели компании» и увеличивать прибыль, поскольку воспринимают коллективные цели только как обогащение руководства компании.
Многих сотрудников пугают возможные сокращения, рост ответственности, необходимость тратить время на обучение, тренинги, совещания (особенно при сдельной оплате труда). Сопротивление сотрудников может свести на нет все усилия компании по внедрению бережливого производства: формальное выполнение требований менеджмента, сознательное саботирование инструкций, снижение мотивации и снижение качества работы, увольнение квалифицированных кадров — риски, с которыми сталкивается практически каждая российская компания при попытке внедрить систему 5S и другие принципы бережливого производства.
Еще более важным и рискованным с точки зрения внедрения системы 5S является отношение руководства предприятия к данной затее. Многие предприятия отказываются от внедрения системы, считая ее просто модной, «раскрученной» западной идеей, не применимой в российских условиях. Отсутствие адаптации этой системы к условиям конкретного предприятия и к традициям, нормам конкретного коллектива, особенно если для внедрения системы привлекаются внешние консультанты и контролеры — тоже сводят усилия на нет. Использование иностранных, особенно японских, терминов усиливает скептицизм сотрудников, снижает доверие к «новомодному феншую» и тормозит появление тех позитивных изменений в организации, для которых создавалась система 5S.
Измерение
Анализ
Улучшение
Контроль
Такая последовательность действий позволяет пройти весь путь от определения проблемы до реализованного решения по её устранению. Таким образом, проблемы устраняются системно, чтобы они больше не появлялись.